Imagine the energy and emissions savings possible in a world where all automotive steel was circular, writes Dean Kanelos
For more than a decade, the global automotive industry has shown an unwavering collective commitment to decarbonisation and greater overall sustainability. Despite these laudable efforts, though, road vehicles still account for fully 15% of the world’s CO2 emissions and remain the fastest-growing source of emissions worldwide. Progress has indeed been made, but plenty of work still needs to be done.
Electric vehicles (EVs) have been the catalyst for much of this progress. But now, as concerns begin to mount that EV adoption rates may be slowing, the industry needs to look beyond what’s coming out of their vehicles’ tailpipes to gain more traction along the road to net zero. The automotive manufacturing process, in particular, is one obvious and significant area of opportunity.
Some 80 million vehicles are now produced annually, requiring more than 112 million tons of materials, including a staggering 67 million tons of steel. Given that, broader industrywide adoption of low-emission recycled steel (circular steel) could represent a significant piece of the decarbonisation puzzle.
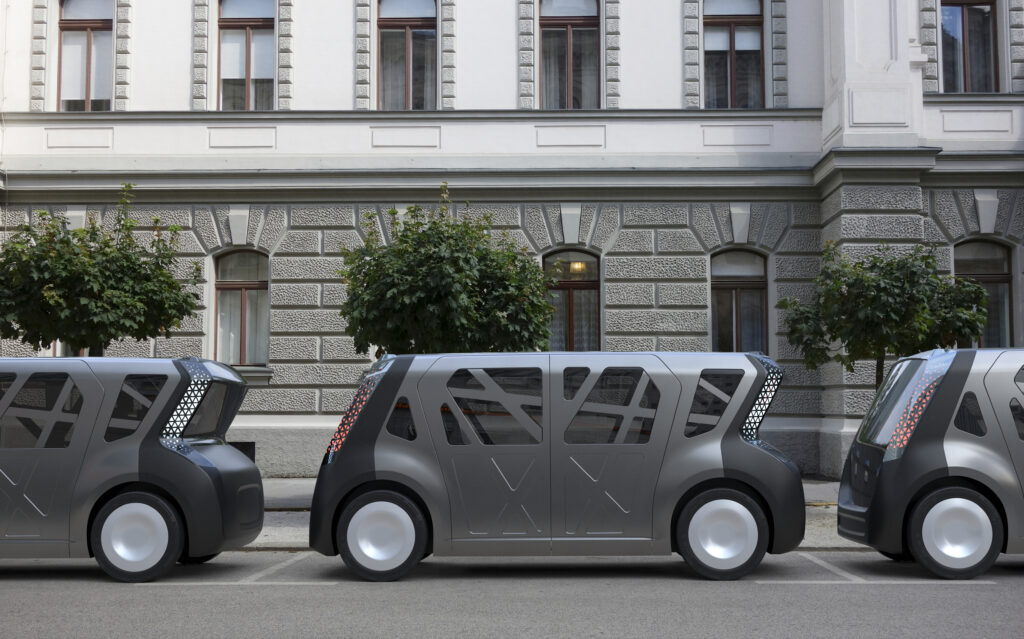
There are two ways to make steel. The traditional method—extracting iron ore from the earth via mining, then refining it in a coal-fired blast furnace and later into steel in a basic oxygen furnace—is highly carbon intensive. The other method—circular steelmaking, which accounts for about 70% of all steel manufactured in the US—uses recycled steel scrap as its primary feedstock, limiting the need to extract raw materials from the earth. And instead of a carbon-intensive blast furnace, it relies on an electric arc furnace (EAF), which consumes far less energy and produces less than one-third the CO2 emissions comparatively. Many US EAFs are even powered in part or fully by renewable energy sources like wind and solar, which multiplies the sustainability benefits.
While OEMs have embraced circular steel to varying degrees, imagine the energy and emissions savings possible in a world where all automotive steel was circular. Although some industry professionals might be surprised to know it, that possibility does indeed exist today. Most steel vehicle components—from drivetrains to suspensions and high-tech components—are now being produced in the US via circular steelmaking.
Even Advanced High-Strength Steel (AHSS), which is increasingly in demand for components such as frame rails, roof bows, rocker panels and A and B pillars, is now manufactured via the circular steelmaking process. Circular AHSS is especially in demand from EV makers because this stronger and more sustainable steel can reduce an EV’s overall weight while also helping overcome challenges related to crash management and intrusion protection.
Despite all of its various sustainability benefits, circular steel is not a magic bullet that will decarbonise the automotive industry on its own. Automakers must also continue to invest in EVs (and hybrids) and promote their adoption while remaining focused on other important initiatives like improving EV battery circularity, driving the broader use of renewable energy sources across all facets of production, and continuing to make their enduringly popular internal combustion engines more efficient to reduce emissions and improve fuel economy.
But given the inextricable relationship between cars and steel—millions and millions of tons of it produced every year—a greater industrywide push toward circular steel is a logical next step along the road to net zero.
The opinions expressed here are those of the author and do not necessarily reflect the positions of Automotive World Ltd.
Dean Kanelos is Automotive Market Development and Product Applications Manager at Nucor Corp, Chairman of WorldAutoSteel and Chairman for the Joint Policy Council of the Auto/Steel Partnership
The AutomotiveWorld.com Comment column is open to automotive industry decision makers and influencers. If you would like to contribute a Comment article, please contact editorial@automotiveworld.com